- HOME
- CSR Activities
- Social Report
- Our Relationship with Customers
Our Relationship with Customers
- An Approach that Considers the End-User’s Point of View
- In Pursuit of Superior Product Quality that Exceeds Customer Expectations
- Global Quality Control and Assurance System
- Quality Assurance System (Traceability Control)
- TC Circles
- Providing Safe Products
- Prevention and Recurrence Prevention Initiatives
An Approach that Considers the End-User’s Point of View
The TS TECH Group is committed to a style of monozukuri that has not only finished vehicle manufacturers, our direct customers, in mind but also feedback from end users, our indirect customers.
The New Product Development Department communicates with end users through a range of approaches and conducts marketing research using survey techniques tailored to specific markets and research targets. In product development, the perception of automobile users is of the utmost importance, and marketing research plays a significant role as a means to assess their needs and match them with TS TECH’s technologies.
Survey results are used for purposes such as customer proposals, model planning, and development of new technology. Although we are a business-to-business company, we do not limit ourselves strictly to “components,” instead striving to create new innovations by conducting forward-looking research and constantly working to become “a company sincerely appreciated by all.”
Main Survey Techniques
- Face-to-face surveys of end users
- Interviews of end users by dealers
- Surveys to verify product usability
- TS TECH’s original online surveys and focus group interviews
- Overseas market surveys and use of big data via research companies
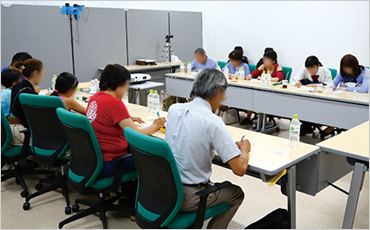
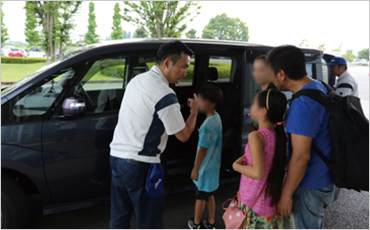
In Pursuit of Superior Product Quality that Exceeds Customer Expectations
Precisely because seats are interior components that end users see with their own eyes and are in physical contact with for long periods while driving, we pursue top-level quality products that always exceed customers’ expectations through our commitment to monozukuri.
Our Group conducts comprehensive quality control, from product planning and development, to the production process at the plant. In particular, when developing a new model, we analyze the quality of existing models and incorporate any issues into the design from the planning and development stages as part of our commitment to improving the specification quality of our products.
As a result of these efforts, we continue to earn high praise in seat quality and satisfaction surveys by a U.S. market research firm.
Quality Assurance System
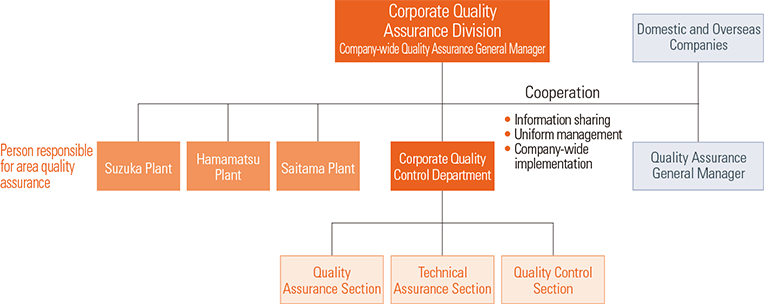
Global Quality Control and Assurance System
The TS TECH Group attaches great importance to quality in our manufacturing at all locations around the globe.
All TS TECH Group sites in and outside Japan have acquired certification in international standards related to quality (e.g., ISO 9001 and ISO/TS 16949), and have established a quality assurance system that can deliver products with the same high level of quality to our customers around the globe.
Meanwhile, our plant manufacturing and quality departments are working together on quality control in the manufacturing process to implement initiatives that ensure and maintain a stable level of high manufacturing quality.
Saitama Plant
Suzuka Plant
Inspection for certification
Quality Assurance System (Traceability Control)
As the TS TECH Group actively promotes the use of common parts across the globe, we are working to enable full traceability of each part through our manufacturing quality control system, and we have a framework in place to assess the spread of quality issues at our domestic and overseas facilities.
In the event of a customer complaint, we can rapidly trace the production history to identify the root cause using our manufacturing quality control system, enabling swift corrective action.
TC Circles
Our own version of quality control (QC) circles, the Group’s TC Circles support Group-wide quality improvements. TC Circle activities are instrumental in the effort to educate employees and strengthen their abilities to manage and resolve quality issues. TC Circles have continued working worldwide to promote the global sharing of concepts and case examples, with the aim of personnel education and the development of new leaders.
To help maintain motivation, TC Circle members (Total number of participating circles in 2019: 483) gather at annual regional competitions in four regions (Japan, the Americas, China, and Asia and Europe) and a world competition that is held every two years. These conventions ultimately help raise quality awareness in all of our employees.
Winning TC Circle team
Providing Safe Products
To provide our customers with safe, reliable products, the TS TECH Group not only observes laws and regulations but also prevents problems from arising through a number of efforts aimed at ensuring product quality and safety.
We check and comply with laws and regulations concerning toxic substances in products. In addition, we check product compliance after quickly establishing supply chains for new materials and provide regular oversight.
For key mass-produced products, we clearly establish priority areas for each component and conduct regular audits that include our suppliers. When developing new products, we perform FTA*1 verification as well as third-party evaluations by experts for key parts with new mechanisms and conduct a potential problem analysis (PPA)*2 for safety.
- *1 Fault Tree Analysis: A method of logically analyzing fault occurrence routes and factors to address reliability or safety problems
- *2 Potential Problem Analysis (PPA): Involves solving problems through the process of identifying and analyzing a problem, devising and executing a solution, and evaluating results
Prevention and Recurrence Prevention Initiatives
We recognize comments and complaints from our customers as information that leads to the further improvement of the TS TECH Group. Via an online system, we have built a network that can confirm complaint data from all of our facilities around the world, and we use it to swiftly resolve complaints and prevent recurrences. Procedures for dealing with defects are clearly outlined in company regulations, and, in the event a defect occurs, we work to ensure that the situation is handled properly by following these regulations.
We also focus on the prevention of various defects by envisioning customers around the globe and a diversity of usage requirements, such as climate differences in each country, and repeatedly implementing tests and evaluations that employ loads that exceed ordinary usage methods. Going forward, we will continue to work hard to provide products that earn customer confidence and satisfaction.